PETG Retraction Calibration
Retraction calibration is needed to reduce stringing and blobbing of hot filament as the hot-end travels from point A to point B. For parts with a small amount of travel, this isn’t as noticeable. For parts that require the hot-end to travel it can be an annoyance to have to trim the excess blobbing and/or melt the fine spider-like stringing post-print. It also reduces the fidelity of the final print as the blobs and string leave imperfections on the surface.
Each material and its manufacturer has varying properties. It takes some trial and error to negotiate the settings that work best.
Currently, I’m calibrating with Prusament PETG. The default profiles DID NOT WORK for retraction from Prusa. It somewhat worked for other prints that have less travel.
Calibration models are found here: [Thingiverse Links] If the STL has a logo on the bottom of the plate use your slicer to fill in the text to speed up the process.
The following parameters were modified incrementally:
Cooling
Filament temperature
Bed Temperature
Z Lift
Retraction speed, length, and lift
Travel Speed
Wipe and Retract on Wipe
Over 40+ prints were performed over a period of 2 weeks. Average humidity is around 50-60%. While the filament was stored in a dry container prior to loading into the printer it simply wasn’t possible to keep the filament dry as I would have to unload/load constantly.
TL;DR; After 40+ prints, the largest effects on retraction performance were temperature and z-lift.
General Rules I Followed
The filename always contained the modified variables. This way you can distinguish the gcode file and reference what parameter was modified
E.g.: [layer_height]-{filament_type[0]}-SPD-[perimeter_speed]-[external_perimeter_speed]-[small_perimeter_speed]-R[filament_retract_length]-[filament_retract_lift]-[filament_retract_speed]-T-[temperature]-[extrusion_multiplier]-[travel_speed]-W-[filament_wipe]-[filament_retract_before_wipe]-C-[fan_always_on]-[min_fan_speed]-[bridge_fan_speed].gcode
The filename always had a sequential number. I would later use a sharpie to label the print and I could reference the print to settings.
Only modify one parameter at a time. i.e. if retraction speed was being changed, I would create 3-4 gcodes with varying retraction speeds. I would then match the final print to see if the parameter changed the quality of the print. If it didn’t, I would reset the parameter back to the default; why change a variable if it has no effect.
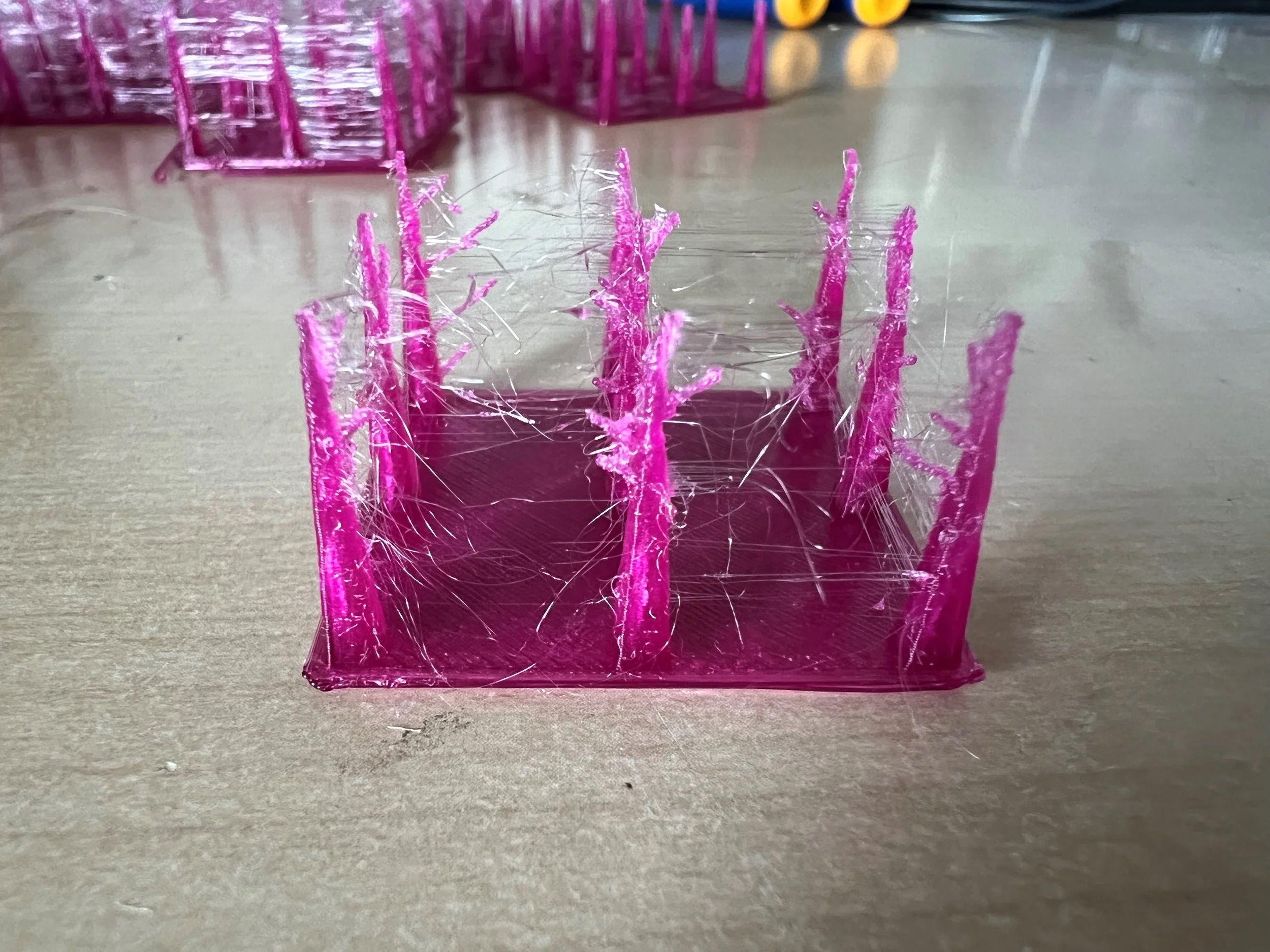


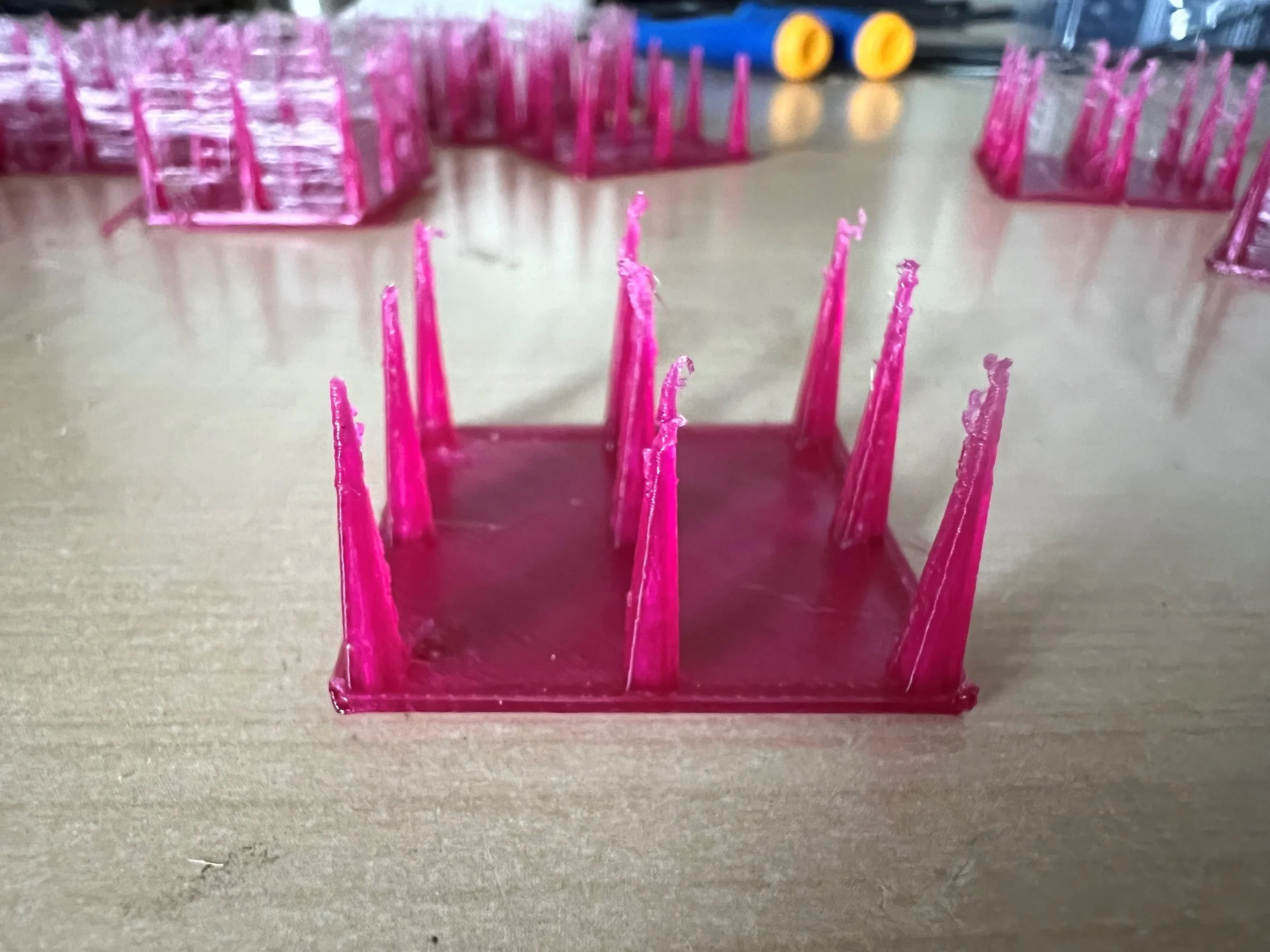
Parameters and Results
Z Lift
I left this at 0.
Many on the internet had good results with zlift. I did not. This was one of the most recommended parameters to change. This did remove long spurs of material at the cost of excessive spider web stringing. My mistake was interpreting this positive change (reduction of spurs of material) as a sign this value had significance and continuing to keep this value modified.
Z-Lift Effects
Fine stringing appears when z-lift was > 0
Retraction Length and Speed, Wipes
I settled on 6mm @ 50mm/s, wipe on retract, 20% amount retraction before wipe.
Minor improvements on retraction tests with speed and length. Many people suggested increasing the filament retraction speed, but this does nothing if your filament has too much pressure in the hotend. The filament will ooze no matter how far you pull the filament back. Also, the higher the retraction speed you can risk the filament slipping or grinding in the extruder.
Bed Temperature
I raised this to 85 degrees.
While PETG filaments vary, the glass temperature of PETG is around 80-85c. I may lower this as I work on the surface finish calibration. PETG is shiny if maintained in a glass transition. PETG will be dull if rapidly cooled. This had very little effect on retraction performance.
Filament Temperature
I lowered the temperature to 225C for all layers and increased the extrusion multiplier to 1.2
The hotter the filament the more it will ooze. I was originally at 245C at an extrusion multiplier of 1. I reduced the temperature and increased the extrusion multiplier to 1.2 to compensate for a cooler filament. This had a lot of impact on blobbing and spider stringing. A lower filament temperature at an EM of 1.0 resulted in under extrusion.
Cooling
No fan for 5 layers, ramp to 30% at layer 10.
Cooling had minor improvements. These parameters are bound to change as I work on overhang performance. Overall, I noticed the PETG doens’t really need much cooling. 5 layers at 0.15mm layer height should be 0.75mm away from the build plate which is a decently thick height. Layer 10 will be 1.5mm from the build plate which my guess was “far enough” from the build plate.
Final Results
This is where I left this project off. Some blobbing near the tips of the print, very little to no spider stringings, very little to none blobbing on the lower sections of the print.